In the girder bridge, the bearing is located on the pier of the superstructure, its role is the load transfer on the bridge structure to the pier, to ensure that the bridge structure and corner displacement requirements. Bridge bearing is an important part of the bridge superstructure and substructure, once the problem occurs, it will have a greater impact on the service life and traffic safety. Therefore, the reasonable installation and use of bridge bearings are very important.
Let Boomarine tell you how to correctly select and install bridge bearings.
1. What is the role of the bridge bearing?
- Transfer the support reaction force of the upper structure, including the vertical force and horizontal force caused by constant load and live load; (transfer load)
- To ensure that the structure in the live load, temperature changes, concrete shrinkage and creep factors such as self-deformation, in order to make the upper and lower structure of the actual force situation in line with the structure of the static force. (adaptation to deformation)
2. What are the two types of bridge bearings according to the possibility of their displacement?
- Fixed bearing transmits vertical force and horizontal force, allowing the upper structure to rotate freely at the bearing but cannot move horizontally.
- The movable bearing only transmits the vertical force, allowing the upper structure at the bearing can both rotate freely and move horizontally.
- The movable bearing can be divided into multi-directional movable bearings (longitudinal, horizontal can move freely) and one-way movable bearings (only one direction can move freely).
3. Arrangement principles of bridge bearings
For sloping bridge-span structures, fixed bearings should be arranged on piers with low elevations.
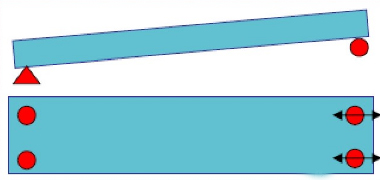
For continuous girder bridge and bridge deck continuous simply-supported girder bridge, in order to make the longitudinal deformation of the whole beam dispersed in the two ends of the beam, it is appropriate to set the fixed bearing near the center of the bridge span.
For a simply supported beam, one end is fixed and one end is movable.
4. What kinds of bridge supports are classified according to materials?
- Simple bearing
- Steel bearing
- Reinforced concrete bearing
- Rubber bearing (plate type rubber bearing, basin type rubber bearing)
- Special bearings (such as vibration-damping bearings, tension bearings, etc.)
(1) Simple bridge bedding bearing
Only applicable to road bridges with spans less than 10m. Bearing free expansion is poor, in order to avoid the main beam end and pier concrete pulling crack, it is appropriate to strengthen the reinforcing steel network at both ends of the bearing parts and the top surface of the pier.
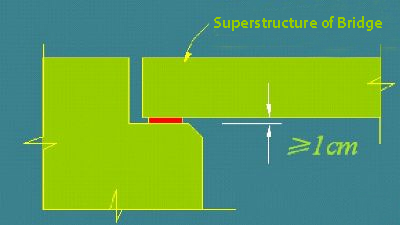
(2) Steel bearing
Steel bearing is relying on the rolling, shaking and sliding of steel parts to complete the displacement and rotation of the bearing
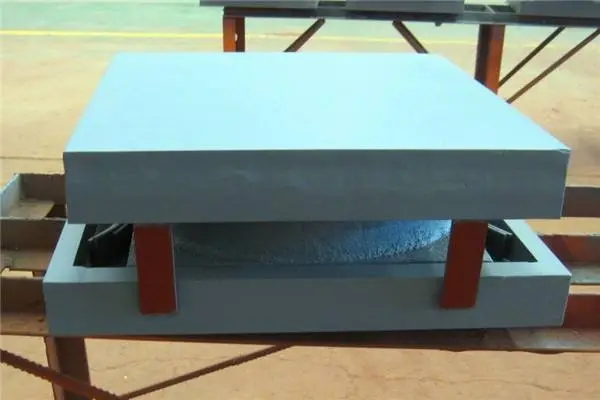
(3) Reinforced concrete bearing (swing column type)
Highway girder bridge with span ≥20, or hanging hole of highway cantilever bridge with span>13m
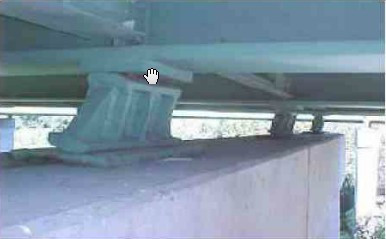
(4) Rubber bearing
Compared with other metal rigid bearings, rubber bearing has a series of advantages such as simple structure, convenient processing, saving steel, low cost, small structure height and easy installation. In addition, the rubber bearing can easily use the deformation of any direction, so it has special adaptability for wide bridges, curve bridges and inclined bridges. The elasticity of rubber can also abate the effect of power on and off the structure, which is also very favorable for earthquake resistance.
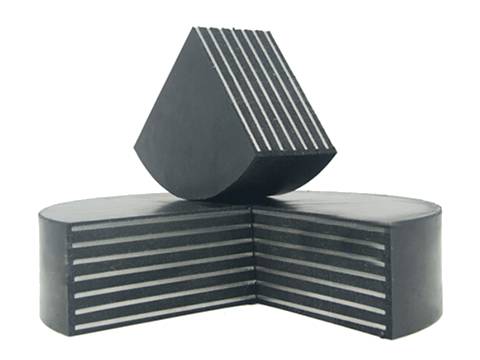
Divided into two categories: plate type rubber bearing and basin type rubber bearing.
â‘ Plate type rubber bearing
Deformation mechanism:Â
- Non-uniform elastic compression realizes rotation;
- Shear deformation realizes horizontal displacement;
- There is no distinction between fixed and movable supports. Obviously, the size of the horizontal displacement and rotational deformation of the rubber bearing is related to the thickness of the bearing.
Performance indicators:Â
- Allowable stress;
- Elastic modulus and shear modulus;
- Allowable shear tangent value.
Scope of application: bridges with bearing reaction force of 3000-10000kN
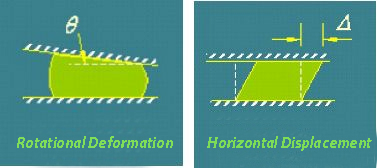
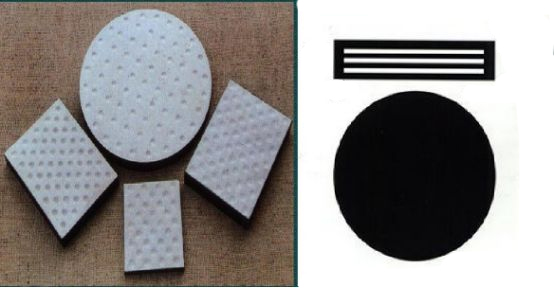
It can overcome the phenomenon of bias and void after installation, and there is no need for leveling at the bottom of the beam for slope bridges.
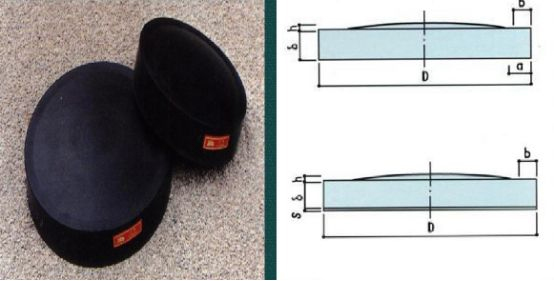
â‘¡ Basin type rubber bearing
Basin type rubber bearing is a kind of rubber bearing that is further improved on the basis of plate type rubber bearing.
The main difference with the plate type rubber bearing: it is not using the reinforcement placed in the rubber to strengthen the rubber, but places the plain rubber in the round steel basin to strengthen the rubber.
The deformation of rubber under pressure is constrained by the steel basin, which is in a three-way pressure state, and as long as the steel basin is not destroyed, the rubber will never lose its bearing capacity. Sealed in the steel basin of the rubber plate, can do moderate uneven compression to achieve rotation, if coupled with PTFE plate and stainless steel plate, can also achieve horizontal displacement.
Basin type rubber bearing can be made into a fixed bearings, can also be made into a movable bearings.
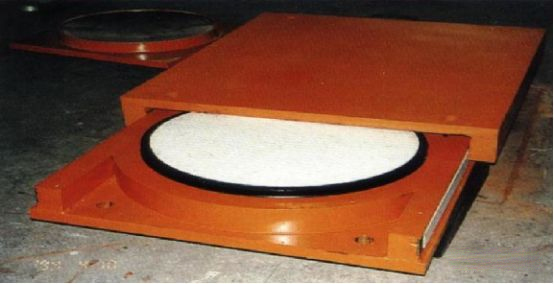
(5) Other bearings
QGZ spherical steel bearing
5. Selection of bridge bearings
- Small and medium span highway bridges generally use plate type rubber bearing.
- Large span continuous beam bridge generally adopts basin type rubber bearing.
6. Installation method of bridge bearings
Bearing into the site should be checked and stored horizontally, shall not destroy the dust cover. Before installing the bearing check the junction pier cover beam top stone size, top surface elevation and the position of the reserved anchor hole, the reserved hole position is not accurate or depth is not enough should be manually chiseled to make it meet the requirements. Use a red pencil to draw the center line of the bearing on the top surface of the bearing pad stone, while drawing the center position on the four sides of the bearing bottom steel plate in order to control the offset during installation. In the bearing on the mat stone under the steel plate to each side of the extension of 3cm area for hair chiseling, remove the surface floating slurry, while the degree of convexity and concavity of the concrete rough surface should not be too large, flatness of 5mm can be.
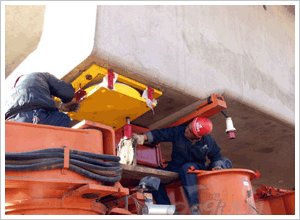
Before the installation of the bearing, the anchor bolts of the lower seat plate of the bearing are installed and fastened, and the bearing is set according to the pre-deviation amount of the bearing installation given by the design. After setting the bearing installation pre-deflection amount, re-adjust the upper and lower seat plate to parallel state and fixed to ensure that the bearing has no initial corner. Then use the crane to lift the bearing to be installed over the cushion stone, manually adjust the bearing direction so that its lower anchor bolts into the corresponding cushion stone anchor holes and slowly decentralized, decentralized to the bearing under the seat plate and cushion stone top surface distance of about 10cm, stop decentralizing the bearing. Prepare to adjust the steel wedge block, wedge block plane for 2cm × 2cm, in the four corners of the bearing each placed a wedge block, devolve the bearing and adjust the steel wedge block and bearing plane position, so that the bearing top surface elevation for the design elevation, axis and design deviation to meet the specifications and surface level.
Bearing accurately in place to the lower part of the grout strength to reach 80% of the design strength before not touching the pressure and moving the bearing. Use 10# channel steel as the outer mold to install reinforcement at the outer 5cm of the lower seat plate of the support, and use dry hard M50 mortar to fill the gap between the bottom edge of the channel steel and the top surface of the mat stone. After the installation of grouting template is completed, the grouting operation is carried out. The gap between the support and the pad stone is filled with fast hard M50 non-shrink high strength mortar by gravity type grouting method. The volume of grout required is calculated according to the space to be grouted, and the grout is first mixed in a storage cylinder according to the ratio, which should be at least 50 cm above the grout plane to be grouted to ensure that the grout area can be filled by gravity flowing grout only. When grouting, use a flat wide grouting pipe to lead the mortar to the center of the lower seat plate of the support, so that it flows freely until the slurry overflows from the four sides of the channel steel and the lower seat plate, grouting is completed.
Do not collide or move the bearing within one day after the support is installed to ensure that the early strength of the mortar is not affected. And after the mortar solidifies, take out the lower height-adjusting wedge of the bearing and fill it with dry-hard M50 mortar.