What is a marine rubber fender and where is it used?
Marine fenders, also known as marine bumpers, are energy buffer devices used on ports or ships to slow down the impact or shock of ships and piers, or ships and ships when berthing or mooring, so that ships and piers avoid damage.
Marine rubber fenders have the characteristics of good elasticity, high energy absorption, convenient maintenance, long service life and convenient mass production. They are widely used in Japan, Europe, America, and Southeast Asian countries. Rubber fenders can not only protect ships and wharves, but also reduce the horizontal load acting on the wharf, improve the berthing capacity of the wharf, and make the newly built wharf lighter and lower the cost.
The size range of rubber fenders is large. It is easier to choose matching vulcanization equipment for regular-size products, but the large-scale vulcanization equipment investment required for super-size products is too high, especially when the product batch is small, it is not cost-effective to invest in large-scale vulcanization equipment.
The solid rubber fender has high energy absorption and reaction force, and also has the advantages of low cost, long service life, simple installation and maintenance, etc. It is a protective device for docks and docks to install more.
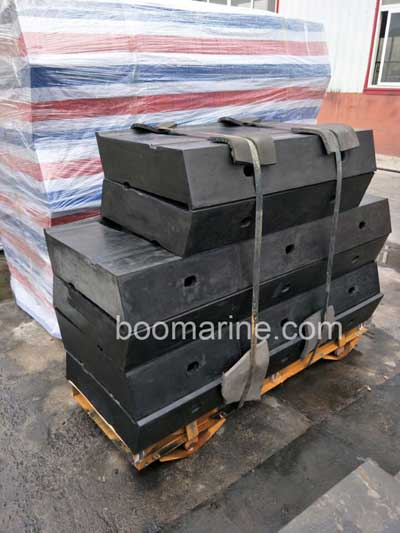
Floating rubber fender is a relatively new type of fender equipment. Compared with solid rubber fender, its main features are: large compression deformation, large energy absorption, small reaction force, self-floating, and easy installation. It is usually used in ship-to-ship, ship-to-wharf barge, docking and other occasions. Due to its self-floating characteristics, it is also particularly suitable for installation on the wharf where the tide level changes greatly.
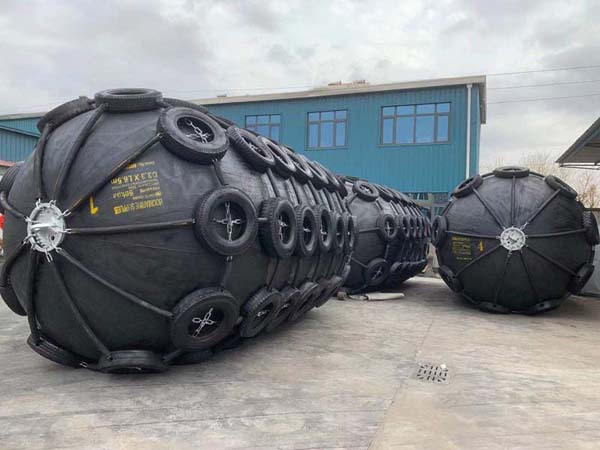
Among them, the foam-filled rubber fender is especially suitable for applications in harsh environments, such as offshore drilling platforms, due to its maintenance-free, long life and other advantages.
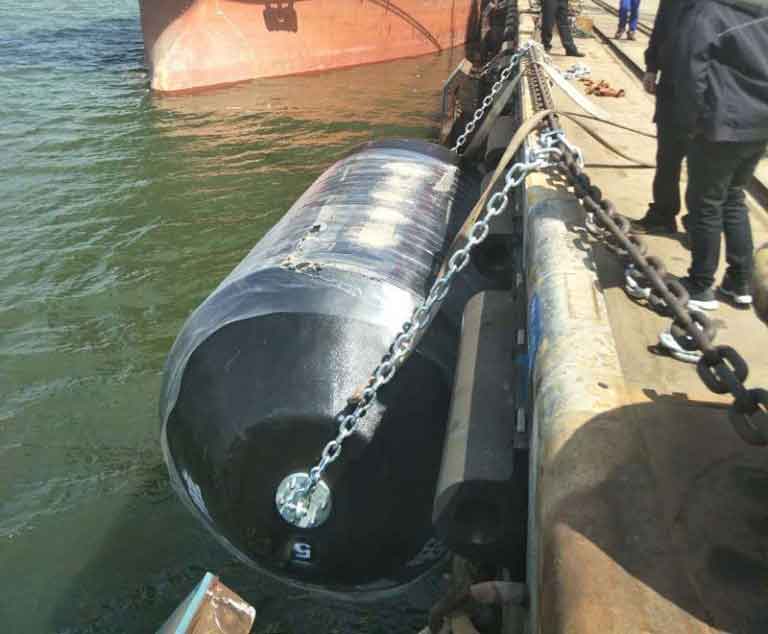
Each type of rubber fender has its own different characteristics, advantages and scope of applications. Let me introduce it to you.
Types and characteristics of marine rubber fenders
(1) Cylindrical rubber fender:
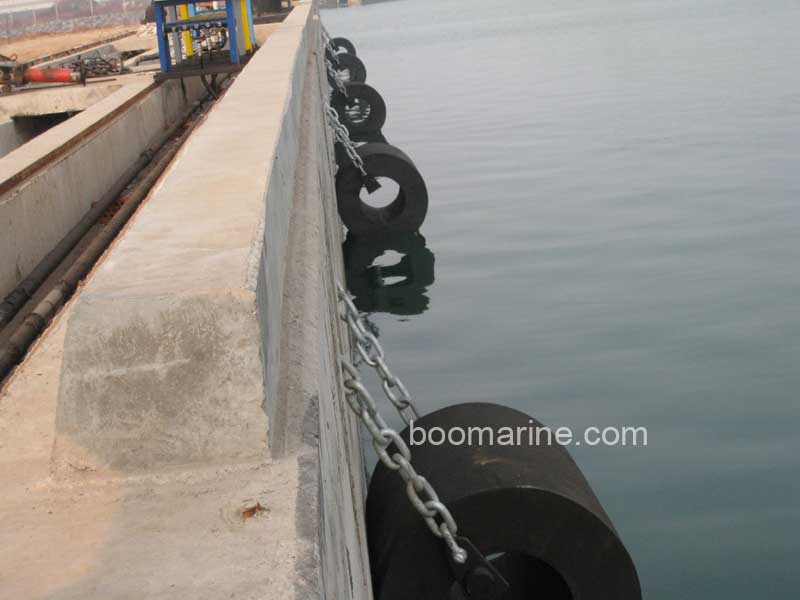
Features: Low reaction force, low surface pressure, and reasonable energy absorption; When berthing, it has strong adaptability to the ship’s rolling and pitching. It is not affected by the size of the ship. It has a wide range of uses and is easy to install and maintain.
It is especially suitable for old-fashioned wharves.
(2) Semi-circular (D-type) rubber fender:
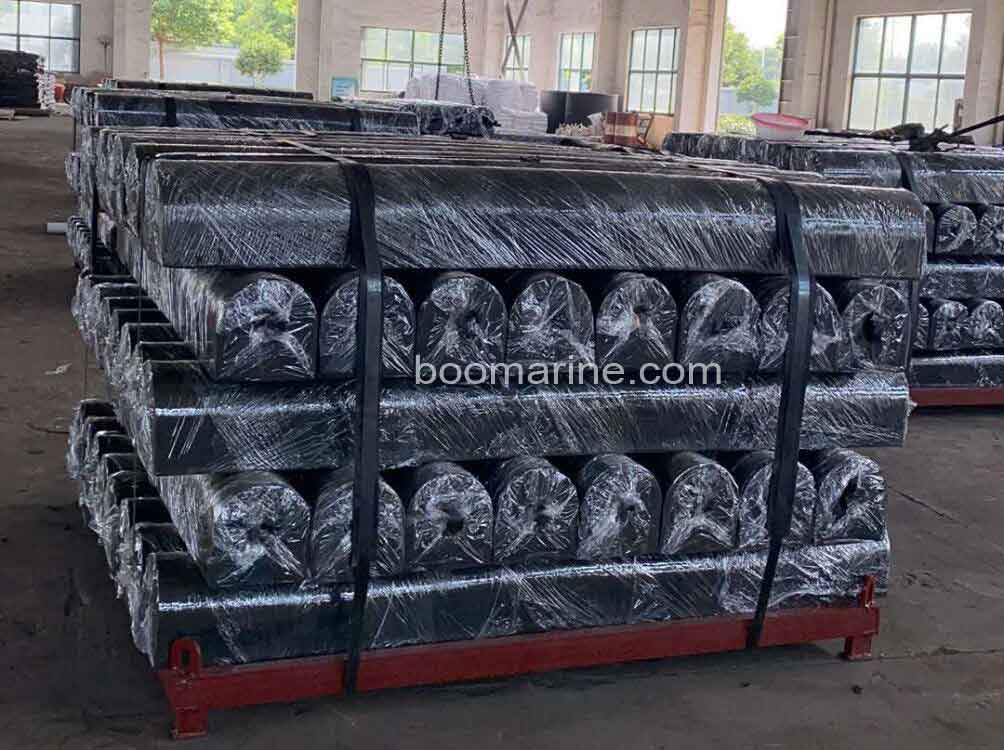
Features: Moderate reaction force, higher energy absorption than cylindrical type; Easy to install.
Due to the small width of the bottom, it is especially suitable for framed wharf and shipboard installation.
(3) DO type rubber fender:
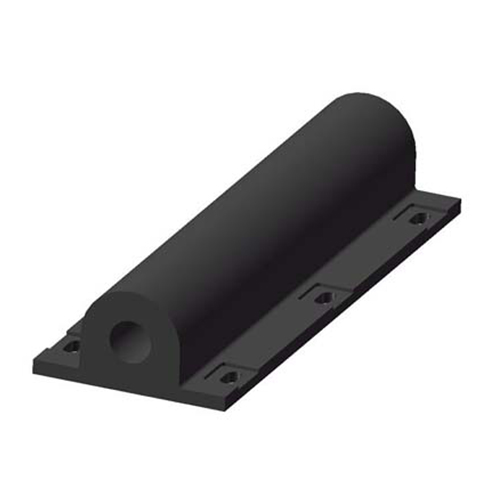
Features: The reaction force and energy absorption are higher than that of D-type fenders; the installation strength and service life are greatly improved compared with D-type fenders.
It is suitable for frame-type wharfs.
(4) Arch (V-shaped) rubber fender:
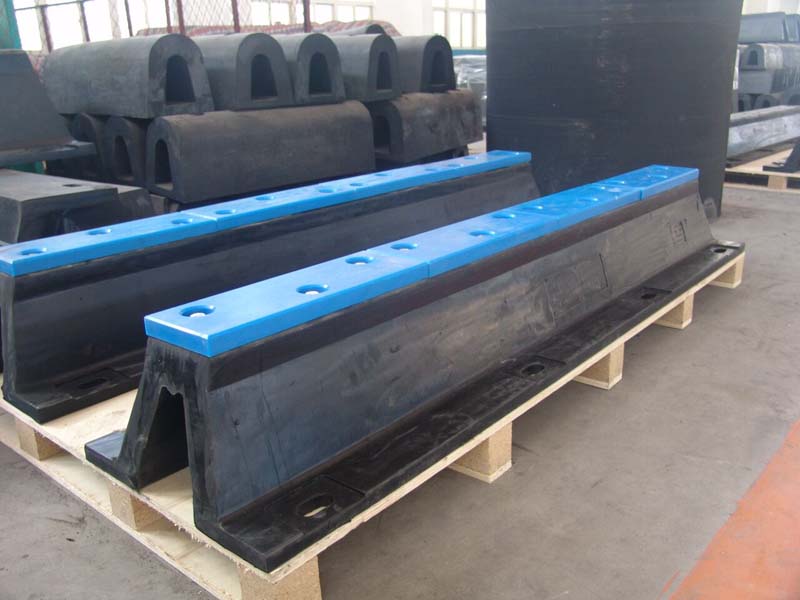
Features: moderate reaction force, high energy absorption; firm and convenient installation.
Applicable to all types of terminals.
(5) DA type rubber fender:
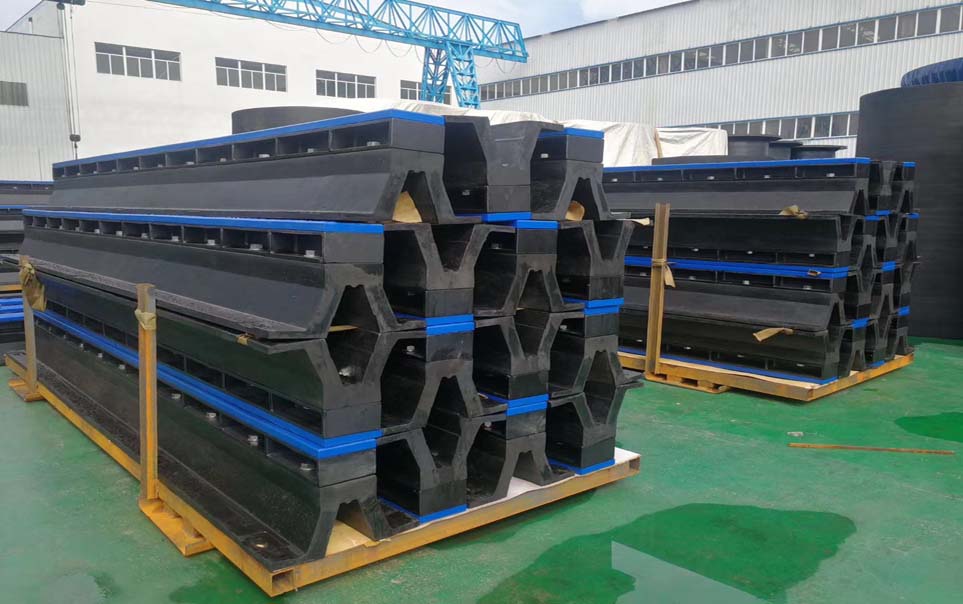
Features: It has the characteristics of high energy absorption and low reaction force; The products have higher stress dispersion and long service life; The front-end guard plate can reduce the surface pressure; The specifications are complete and the installation methods are diverse; the replacement is convenient.
It is suitable for framed wharf and shipboard installation.
(6) Drum rubber fender (cell rubber fender):

Features: Low reaction force, high energy absorption. Surface pressure below 25 tons/m2. Small reduction in mechanical properties of inclined compression. ∏-type rubber fender, features low reaction force, high energy absorption, easy to install.
Generally suitable for large and medium-sized wharfs.
How many rubber fenders should I install on the boat?
The number of rubber fenders depends on the size of the hull. Since the space on any ship is limited, ships of different sizes need to stock different numbers of fenders. For boats up to 10 meters in length, the general rule of thumb is to have two fenders on each side. You can use one or two replacement fenders. On ships over 10 meters, it is best to equip 3-4 fenders on each side, as well as one or two replacement fenders. The side fenders should be in place for docking, but you may find that you need spare fenders to help counteract the tumbling swells or strong winds that secure you to the dock or seawall. Here, in many cases, fenders with more than one shape or type will come in handy.
What are the standards of rubber fender?
The industry standards adopted for solid rubber fenders are “HG/T 2866-2016 Rubber Fenders” and “GB/T 21537-2008 Cone Rubber Fenders“.
The domestic industry standards for inflatable rubber fenders are “CB-T 3948 Marine Inflatable Rubber Ball” rubber fenders and the international ISO standard ISO17357: 2002 “High pressure Floating pneumatic rubber fenders“. Filled floating rubber fender is a new product, and there is no international standard or industry standard.
If you still don’t know how to choose the right rubber fenders, you can contact us at any time. Boomarine is a leading supplier in the design and manufacture of advanced fender systems. Regardless of your work needs and environmental conditions, we provide the best-promised materials to achieve low maintenance and long life. To get the best solution and make your fender meet your specifications, please feel free to contact us.