1. What is a buoy?
A buoy is an object floating in water, which is anchored at a designated location and used as a locator or a warning point for a vessel as a navigational aid. It is made of strong and tough polymer polyethylene and other materials. It has good weather resistance and impact resistance, and can resist ultraviolet rays, frost, and seawater chemicals. Corrosion such as oil stains and so on. Buoy is usually bright in color (fluorescent), widely used, and is often set in places where it is difficult or inappropriate to set up fixed navigation aids.
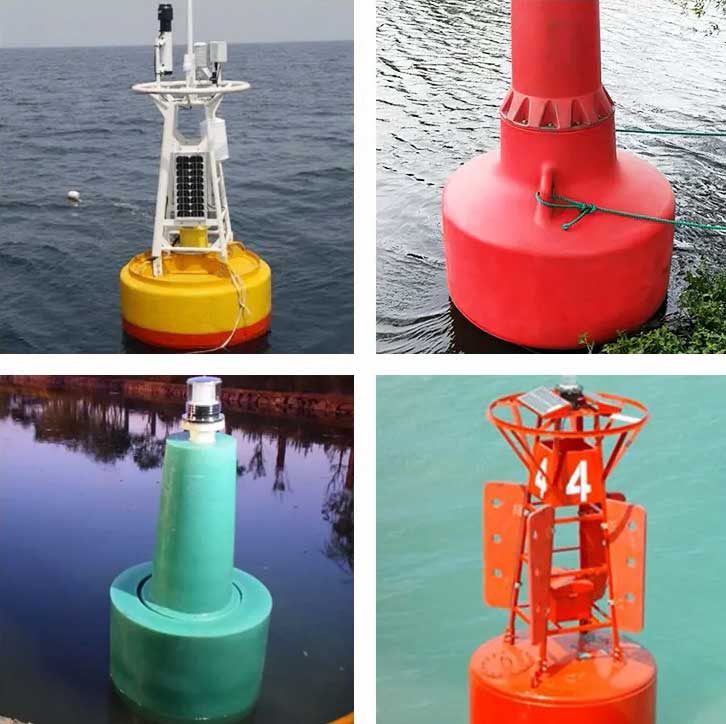
There are many types of buoys. Buoys equipped with lamps are called light buoys, which are used for navigation aids in day and night navigable waters are called navigation buoys. Some buoys are also equipped with radar transponders, radio beacons, fog signals and marine survey instruments. Another kind of buoy is a closed cylinder floating on the water surface, and the lower part is fixed with an iron anchor, which is used for mooring ships or as navigation marks, etc., also known as mooring buoys.
Due to its good impact resistance, performance and reasonable price, the buoy has gradually become popular around the world. The most important thing is that it is environmentally friendly and basically maintenance-free.
2. Buoy Material
(1) Function and requirements
The buoys are usually installed outside the deep water marine risers, mainly to save weight for the rigid risers in the deep sea. In addition, since the riser works in the harsh environment of the sea for a long time, these buoys fixed on its outer surface can also play a good role in column protection. High temperature and high pressure (HP/HT) environments place higher thermal insulation requirements on marine risers to prevent the formation of waxes and hydrates as the product cools along the pipeline. In addition to the design of the marine riser, the external float can also play a good role in thermal insulation protection. Therefore, according to the performance and service conditions of the deep-water technical marine riser, its external buoy material must meet the following requirements:
- The density of the buoy material should be as small as possible, so that it can provide as much buoyancy as possible per unit volume, thereby improving the working performance of the marine riser;
- Can withstand the required hydrostatic pressure (the water pressure increases by 1MPa for every 100m diving depth of the marine riser), and will not cause damage within the specified depth of use, that is, the pressure resistance condition;
- Low water absorption and bulk modulus of elasticity enable it to provide stable buoyancy under large water pressure, ensuring the safe and reliable operation of marine risers. At the same time, it is necessary to consider the overall handling, load and use of the riser and the buoyancy material. During the use of the buoyancy material, safety and reliability problems such as cracks, splits and loss of buoyancy may occur. The reinforced floating material can be quite strong. For example, two layers of Kevlar glass fiber reinforced plastic are coated on the surface of the floating material and the material is reinforced inside, which can increase the strength of the floating material and make it safer to use.
(2) Material classification and characteristics
The selection of buoy materials is very important for the entire underwater operation system. Usually, there are mainly three kinds of polyurethane foam materials, copolymer foam materials and syntactic foam materials.
- Polyurethane Foam
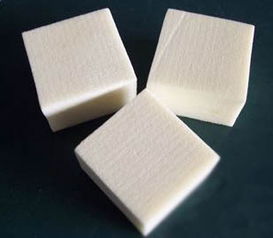
The cost of the buoy material made of polyurethane foam material can be well controlled, but it is mainly used on the water surface and the depth below the water surface is less than rice water.
This foam material used underwater must be completely covered by other materials to ensure its complete isolation from water, because this foam is absorbent, and if it is in direct contact with seawater for a long time, the material will absorb water under the action of water pressure.
- Copolymer Foam
Co-foams are rigid closed-cell foams that can withstand seawater static pressure without the need for complete shell closure. Such foams are usually processed into slabs or sheets, but there are a number of critical factors that must be considered before processing and testing.
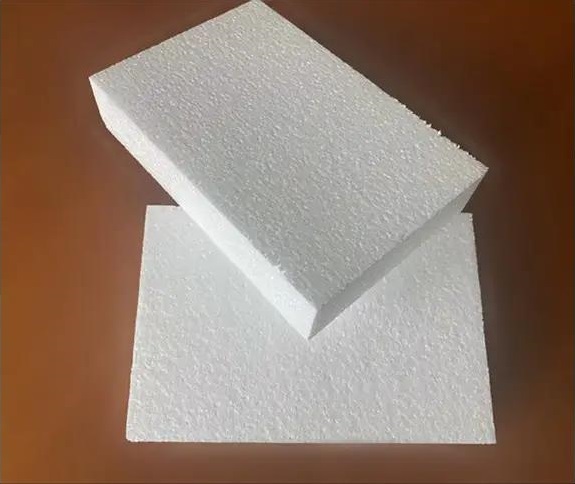
Low-density foams of this material are suitable for short-term applications. This material will undergo plastic creep, deformation and volume reduction if used in a continuous hydrostatic load environment for a long period of time. Therefore, buoyancy is reduced. The density of the material ranges from 40 to 400kg/m3, and the maximum working depth can reach 600 meters.
- Syntactic Foam
Syntactic foam is the latest generation of buoy material that has the advantage of maintaining sufficient strength at very low densities, with a high compressive strength-to-weight ratio, low creep and low water absorption. This makes it possible to provide buoyancy and protection for equipment in the deep sea. The riser buoy core is basically made of this material.
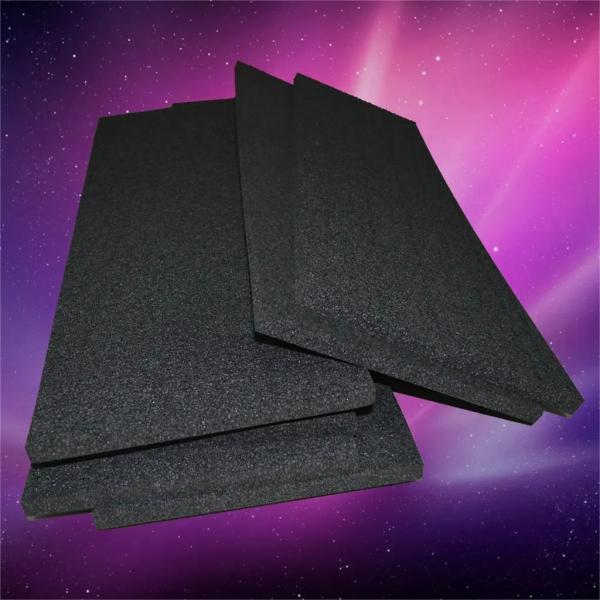
The low density of this material is mainly due to the uniform dispersion of a large number of hollow glass microbodies in the matrix material. The surface of these microspheres has been optimized, and after advanced chemical processing technology, they are organically integrated with the material, which further strengthens the overall material properties. Hollow glass microspheres are spherical hollow particles with a gray or gray appearance and a hard shell. Its main components are SiO2 and Al2O3, and the wall thickness is 8% to 10% of its diameter. The requirements for the base material are strong adhesion, low water absorption, excellent thermal and electrical properties, and epoxy resin is the first choice. Because of its good adhesive strength, thermal stability, dimensional stability and processability are outstanding. In the process of material synthesis, diluents, curing agents and surface modifiers are also added. After a large number of hollow glass micro-bodies with a diameter of 20 to 150 microns are introduced into the matrix, the density of the entire material will be reduced to between 0.46 and 0.65. The material at this time is called pure syntactic foam.
To further reduce the specific gravity of the material, some larger hollow spheres are added. These microsphere materials are different from the glass microspheres described above, which are high strength fiber composite spheres. They are larger in size, from 10mm to 110mm in outer diameter. The specific gravity of the syntactic foam after containing the three components can reach between 275 and 560kg/m3, and the material containing the three components is called syntactic foam.
The density of pure syntactic foam material ranges from 380kg/m3 to 650kg/m3 and can be applied to any seawater depth.
Synthetic syntactic foams have densities ranging from 275kg/m3 to 560kg/m3 and are typically used in seawater up to 4000 meters underwater. Syntactic foams are the most widely used in deep-water operating environments. Typical syntactic foam properties are shown as follows fig.
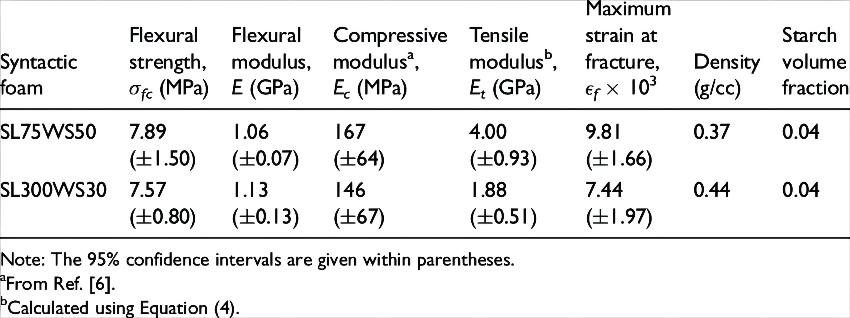
The same material varies due to different application conditions. In order to achieve the best performance of the buoy material, different types of buoy materials can be finally designed and selected according to the different depths of use of the buoy material and combined with the actual application.
3. Structure of Buoys
There are some situations that need to be considered in the design stage of the buoy structure, mainly including the following:
- The buoy shell is generally formed by an integral mold, and then the foam material is injected into the package. The surface material is generally made of fiber-reinforced material, which has a strong ability to resist wear and impact. The hard surface of the buoy made of this material can withstand water pressure in deep water.
- In some cases, in order to further increase the strength of the buoy block, a layer of reinforcing mesh is added between the shell of the buoy block and the synthetic foam material.
- In order to prevent the bending load generated by gravity in the horizontal plane from being transmitted to the buoy too much during the installation or lifting of the riser, two flexible pads are consciously designed in the inner circumference of the buoy block.
- The upper and lower ends of most of the buoys are designed as sleeves. One end of each set of sleeves is designed as a concave end, and the other end is designed as a convex end, so that after the sleeves are installed, each group of buoys independently forms a buoy string. It is beneficial to evenly distribute buoyancy when doing some manipulations.
- After the buoy block is processed, the outer circumferential surface of the buoy block is often designed to be a plane in order to facilitate stacking.
- The main function of the buoy is to provide buoyancy for the riser in the water. Each buoy block should be installed and fixed in a specific riser section, and the shape of its internal groove must correspond to the actual structure of the riser.
- For the buoys in different water depths of the district, the buoys are distinguished by different colors.
4. Buoy Clamping System
There are two methods for securing the buoy to the riser: internal locking system or external circumferential band system.
The internal locking system consists of 4 bolting systems, each individual system includes a stud bolt or a single stud bolt (the bolt can be made of stainless steel or titanium according to actual needs), a washer, Anti-loose split nuts, and stiffeners.
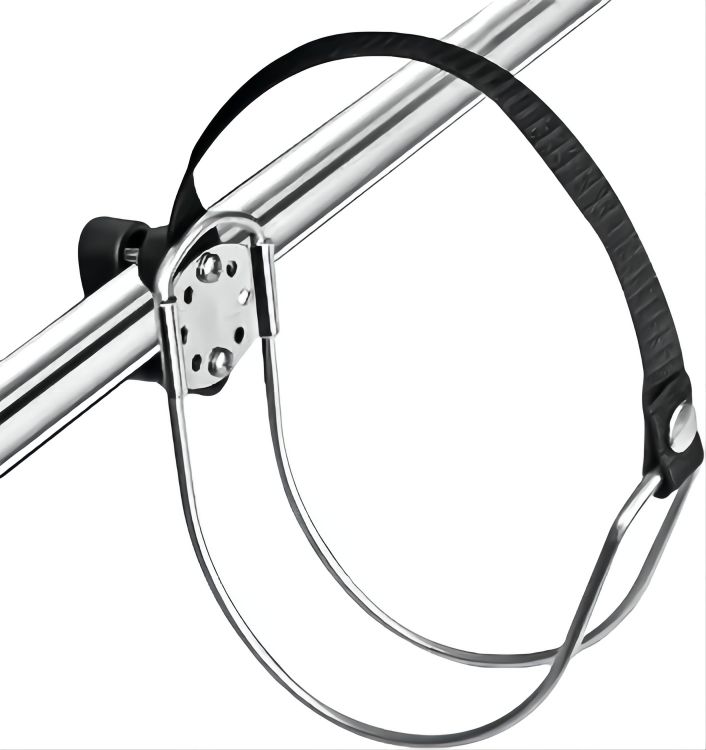
The outer circumferential belt system is mainly composed of high-strength fiber belt and stainless steel frame and stud connection structure. According to the difference between the actual riser and floating structure, the clamping structure is different.
5. Buoy level gauge
The buoy level gauge consists of four basic parts: buoy, spring, magnetic steel chamber and indicator.
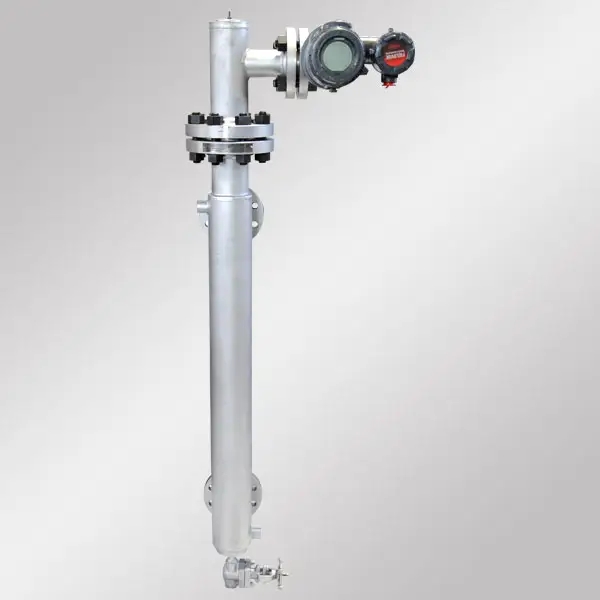
A buoy submerged in liquid is subjected to a combination of downward gravity, upward buoyancy and spring force. When these three forces reach equilibrium, the buoy is at rest in a certain position. When the liquid level changes, the buoyancy of the buoy is changed accordingly, and the equilibrium state is broken, causing the elastic force to change, that is, the expansion and contraction of the spring, to achieve a balance. The expansion and contraction of the spring cause it to displace with the rigidly connected magnetic steel. In this way, the liquid level is indicated by the magnetic induction element and the transmission device in the indicator. The instrument of the limit switch can realize the alarm function of the liquid level signal.
The above are the 5 basic knowledge about buoys. If there is still something you don’t understand, please feel free to contact us. As a professional marine equipment supplier, Boomarine can provide you with tailor-made solutions.