The primary function of the roller fairlead is to guide and protect mooring lines as they are tensioned and released during berthing, unberthing, and other ship maneuvers. Ensuring the safety and security of both the vessel and the port facility needs the efficient and reliable operation of a roller fairlead. Given the demanding conditions of maritime environments, the choice of materials for roller fairleads is subjected to a wide range of stresses, including abrasion, corrosion, and heavy loads. The materials used must possess a combination of properties to withstand these challenges and provide long-term service. There is an introduction to the kinds of materials for the roller fairlead.
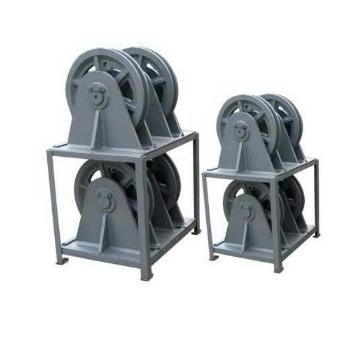
Main Materials for Roller Fairleads
Some suppliers like Boomarine will provide many advanced materials in roller fairlead construction, but there are also some traditional materials you can choose from.
Metallic Materials
Steel
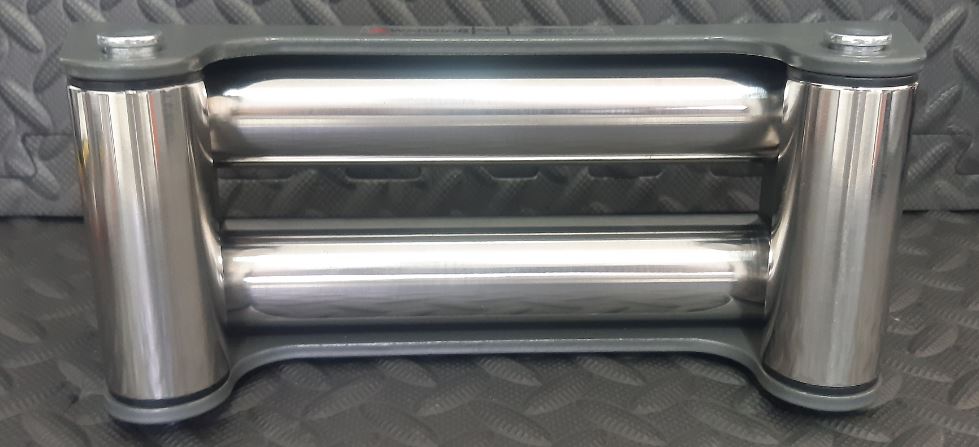
The high tensile strength of steel ensures that the fairlead can withstand the considerable forces exerted by mooring lines during ship maneuvers. Additionally, the hardness of steel provides excellent wear resistance, prolonging the service life of the component.
Different types of steel are employed in roller fairlead manufacturing, each offering unique properties. For instance, stainless steel is often used in marine environments due to its corrosion resistance. Alloy steels, such as those containing chromium and molybdenum, are selected for their enhanced strength and toughness. Cast steel is commonly used for complex shapes and large-scale components.
Cast Iron
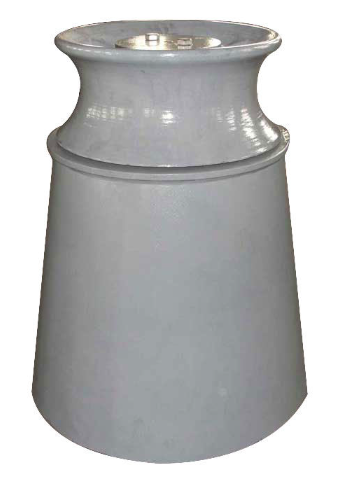
Cast iron is a relatively inexpensive material that is easy to cast into complex shapes. Its good compressive strength makes it suitable for applications where the primary load is compressive, such as supporting the weight of the roller. However, cast iron has lower tensile strength and is more brittle than steel, limiting its use in high-stress applications. Cast iron fairleads are often found on smaller vessels or in less demanding environments.
Other Metals (e.g., Stainless Steel)
Stainless steel is highly resistant to corrosion and oxidation, making it an excellent choice for marine applications. The passive layer on the surface of stainless steel provides excellent protection against saltwater and atmospheric corrosion. Stainless steel fairleads are commonly used on luxury yachts, offshore platforms, and other vessels operating in harsh environments.
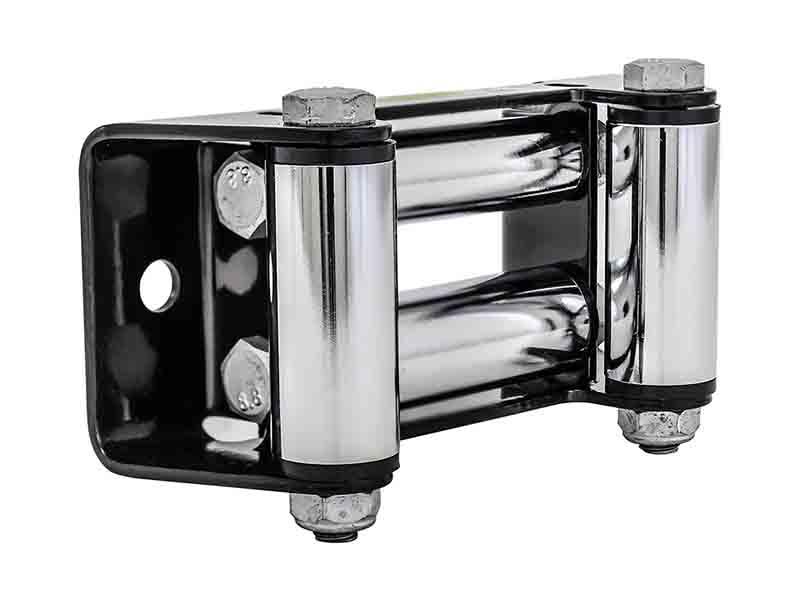
Non-Metallic Materials
Rubber
Rubber is often used as a coating on the outer surface of roller fairleads to provide friction and protect mooring lines. The rubber coating helps to grip the mooring line, preventing it from slipping. Additionally, rubber can absorb some of the energy from the mooring line, reducing wear and tear on both the line and the fairlead. The choice of rubber compound depends on the specific application, considering factors such as temperature range, chemical resistance, and abrasion resistance.
Plastics
Nylon is a common engineering plastic used in roller fairleads due to its high strength-to-weight ratio, good wear resistance, and excellent resistance to chemicals and impact. Nylon fairleads are often used on smaller vessels and in applications where weight is a critical factor.
Other plastics, such as polyethylene and polypropylene, may also be used in roller fairlead construction. These materials offer excellent chemical resistance and good wear resistance, but they may have lower strength and stiffness compared to nylon.
Composite Materials
Composite materials offer a wide range of properties that can be tailored to specific applications. By combining different materials, such as fibers and resins, engineers can create components with high strength, stiffness, and corrosion resistance. For example, a composite fairlead might consist of a fiberglass-reinforced epoxy matrix with a stainless steel insert. This combination provides excellent corrosion resistance, high strength, and a lightweight structure.
Composite fairleads are increasingly being used in marine applications, particularly for larger vessels and offshore structures. The ability to tailor the properties of composite materials makes them well-suited for demanding environments.
Key Considerations of Material Selection for Roller Fairleads
The choice of material for a roller fairlead is a critical decision that significantly impacts the performance, durability, and overall cost of the component. Several factors must be considered when selecting the appropriate material, including the operating environment, the type of vessel, and the frequency of use.
Operating Environment
- Marine Environment: The marine environment is particularly harsh, with high levels of salinity, moisture, and exposure to corrosive substances. Materials used in roller fairleads for marine applications must be highly resistant to corrosion. Stainless steel, due to its passive layer, is a common choice for marine environments. Other corrosion-resistant alloys and coatings can also be employed.
- Climatic Conditions: Extreme temperatures can affect the performance of materials. In cold climates, materials must be able to withstand low temperatures without becoming brittle. In hot climates, materials must be resistant to thermal expansion and degradation. Additionally, materials must be able to withstand exposure to ultraviolet radiation, which can degrade certain plastics and rubbers.
Vessel Type and Operational Requirements
- Vessel Size and Type: Large cargo ships and tankers often require heavy-duty roller fairleads capable of handling large mooring lines under significant tension. These vessels may require materials with higher strength and durability. Smaller vessels, such as fishing boats, may have less demanding requirements and can use lighter, more cost-effective materials.
- Frequency of Use: Roller fairleads on vessels that are frequently used or subjected to high loads will require materials with better wear resistance and fatigue properties. For example, a tugboat that frequently maneuvers in tight spaces may require roller fairleads with a more robust design and materials that can withstand frequent impacts.
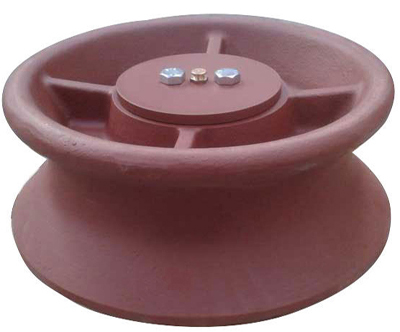
Key Material Properties
- Corrosion resistance: Prevents rust and deterioration.
- Strength and durability: Withstands mooring line forces.
- Wear resistance: Mitigates friction.
- Impact resistance: Handles sudden shocks.
- Temperature resistance: Operates in extreme conditions.
- Weight: Minimizes vessel weight.
- Cost-effectiveness: Balances initial cost and service life.
Material Options
- Stainless steel: Corrosion-resistant, strong, and durable.
- Aluminum alloys: Lightweight and corrosion-resistant, but less strong than steel.
- Cast iron: Cost-effective, easily castable, but less strong and brittle.
- Composite materials: Versatile, customizable, and strong.
- Plastics: Lightweight and corrosion-resistant, but limited strength and temperature resistance.
- Rubber: Provides friction and protects mooring lines.
The Final Word
A variety of materials are commonly used in the construction of roller fairleads, each with its own unique properties and advantages. The most common materials include steel, cast iron, stainless steel, aluminum alloys, composites, and plastics reinforced with fibers such as fiberglass or carbon fiber. The choice of material is determined by a number of factors, including the operating environment, the type of vessel, and the specific requirements of the application. Factors such as corrosion resistance, strength, durability, wear resistance, and impact resistance must be carefully considered.
By carefully considering the factors discussed in this paper or consulting the professional roller fairleads supplier Boomarine directly, you can select the most suitable material for a given application, thereby enhancing the safety, efficiency, and longevity of maritime operations.