A roller fairlead is specialized marine equipment designed to guide ropes, wires, or cables, reducing friction and preventing wear as they are paid out or hauled in. You might have grasped the basic information about roller fairlead. This article focuses on the specific precautions that should be taken when using roller fairleads in varying weather and sea conditions. From the relative calm of a sunny day to the challenges posed by rough seas, extreme temperatures, and icy conditions!
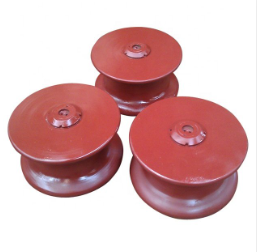
A. Precautions in Calm Seas and Normal Weather
Standard Operating Procedures
- Pre-Operational Checks: Before any operation involving the roller fairlead, a visual inspection should be conducted. This includes verifying that the fairlead is securely mounted and that all components are in good working order. Check for any signs of damage or corrosion.
- Line Handling: Ensure that lines are properly led through the fairlead to prevent unnecessary stress or twisting. Avoid sudden jerking or shock loading of the lines. Maintain a steady and controlled speed during hauling or paying out operations.
- Monitoring: Even in calm conditions, operators should monitor the fairlead and lines during operation. Listen for any unusual noises or vibrations that could indicate a problem. Visually inspect the lines for signs of chafing or wear.
Routine Maintenance and Inspection
Regular maintenance and inspection are critical, even in ideal conditions, to prevent future problems and ensure the continued safe operation of the roller fairlead.
- Lubrication: Proper lubrication is essential to minimize friction and wear. Consult the manufacturer’s recommendations for the appropriate type of lubricant and lubrication frequency. Pay particular attention to lubricating the rollers, bearings, and any other moving parts.
- Wear and Tear Checks: Regularly inspect the rollers for signs of wear, such as flat spots, grooves, or pitting. Examine the frame for cracks, distortion, or corrosion. Check all other components, including bolts, nuts, and welds, for any signs of damage or loosening.
- Securing Mechanism Inspection: Verify the integrity of the fairlead’s securing mechanisms. Ensure that the fairlead is securely attached to its mounting point and that all bolts and fasteners are tightened to the correct torque specifications. Check for any signs of corrosion or damage to the securing components.
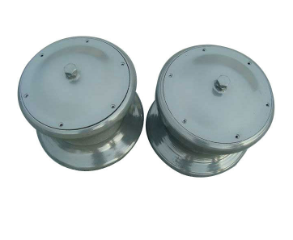
B. Precautions in Rough Seas and Heavy Weather
Challenges Posed by Rough Seas
Rough seas and heavy weather significantly increase the stress on roller fairleads and associated equipment. The dynamic nature of wave action introduces several challenges:
- Increased Stress: Wave motion creates larger and more unpredictable forces on the lines passing through the fairlead, leading to increased stress on the rollers, frame, and securing mechanisms.
- Dynamic Loads: The constantly changing wave height and direction result in dynamic loads, meaning the forces on the fairlead are not static but fluctuate rapidly. This can lead to fatigue and accelerated wear.
- Potential for Shock Loading: Sudden large waves can cause shock loading, where the fairlead and lines experience a sudden and intense force. This can cause significant damage or even failure.
Specific Precautions
- Enhanced Securing: In rough seas, it is crucial to ensure that the fairlead and all associated equipment (ropes, cables, etc.) are secured even more firmly than in calm conditions. This may involve using additional securing devices or tightening existing ones to a higher torque specification.
- Reduced Operational Speed: Reducing the speed of operations involving the fairlead minimizes the impact of dynamic loads. Slower movements allow for better control and reduce the risk of shock loading.
- Increased Monitoring: Constant monitoring of the fairlead, lines, and surrounding area is essential. Operators should be vigilant for signs of excessive stress, such as unusual noises, vibrations, or visible damage.
- Enhanced Personnel Safety: Additional safety measures are necessary for personnel working near the fairlead in rough seas. This may include restricting access to hazardous areas, providing additional safety briefings, and ensuring that all personnel wear appropriate PPE.
Impact of Wave Height and Direction
The height and direction of waves significantly influence the forces acting on the fairlead. Larger waves generate greater forces, while the wave direction determines the angle of attack on the fairlead. Operators should be aware of the prevailing wave conditions and adjust their procedures accordingly.
C. Precautions in Extreme Temperatures
Extreme Heat
- Effects on Lubricants and Materials: High temperatures can cause lubricants to break down and lose their lubricating properties. They can also affect the strength and integrity of some materials used in the fairlead’s construction.
- Recommended Lubricants: Use high-temperature lubricants specifically designed for the operating conditions. Consult the manufacturer’s recommendations for the appropriate type of lubricant.
- Increased Inspection Frequency: More frequent inspections are necessary in extreme heat to check for signs of lubricant degradation, material damage, or excessive wear.
Extreme Cold
- Challenges of Ice Formation: Ice formation can obstruct the fairlead’s rollers and impede the movement of lines. It can also add weight and stress to the system.
- Ice Prevention Methods: Several methods can be used to prevent ice buildup, including heating elements installed on the fairlead, regular de-icing procedures, and the application of anti-icing compounds.
- Increased Material Brittleness: Some materials become more brittle at low temperatures, making them more susceptible to cracking or breaking under stress.
- Recommended Lubricants: Use low-temperature lubricants that remain fluid and effective in cold conditions. Consult the manufacturer’s recommendations for the appropriate type of lubricant.
D. Precautions in Icy Conditions
Challenges of Ice Accumulation
Ice accumulation on roller fairleads and ropes/cables presents several significant challenges:
- Impeded Movement: Ice buildup can obstruct the free rotation of the fairlead’s rollers, hindering the smooth passage of ropes and cables. This can lead to increased friction, strain, and potential damage to both the fairlead and the lines.
- Added Weight and Stress: Ice accumulation adds significant weight to the ropes and cables, increasing the stress on the fairlead and its securing mechanisms. This added weight can also make handling the lines more difficult and dangerous.
- Reduced Flexibility: Ice can make ropes and cables stiff and less flexible, making them more difficult to handle and increasing the risk of kinking or damage.
- Interference with Operation: In severe cases, ice buildup can completely prevent the fairlead from operating correctly, rendering it useless until the ice is removed.
Specific Procedures for Ice Removal
- Mechanical Removal: Physically removing ice using tools like ice picks, scrapers, or hammers is often necessary. Care must be taken to avoid damaging the fairlead or the ropes/cables during this process.
- De-icing Agents: Applying de-icing agents, such as specialized chemicals or heated water, can help to melt the ice and facilitate its removal. Ensure that any de-icing agent used is compatible with the materials of the fairlead and ropes/cables.
- Heating Elements: Installing heating elements on the fairlead can help to prevent ice buildup or melt existing ice. These elements should be designed for marine environments and properly insulated to prevent electrical hazards.
- Preventative Measures: Applying anti-icing compounds to the fairlead and ropes/cables before ice formation can help to prevent ice from adhering in the first place.
Specialized Inspections After Icy Conditions
After periods of icy conditions, it is crucial to conduct specialized inspections of the roller fairlead and associated equipment. These inspections should include:
- Thorough Cleaning: Remove all remaining ice and debris from the fairlead and ropes/cables.
- Detailed Inspection: Carefully inspect all components for signs of damage, such as cracks, distortion, or excessive wear. Pay particular attention to the rollers, bearings, and securing mechanisms.
- Lubrication Check: Check the lubrication of all moving parts and reapply lubricant as needed. Ice and ice removal procedures can wash away existing lubrication.
- Line Inspection: Inspect the ropes and cables for any signs of damage, such as cuts, abrasions, or broken strands. Replace any damaged lines immediately.
Summary
Ensuring the safe and efficient operation of roller fairleads requires a comprehensive understanding of the challenges posed by varying environmental conditions. As this article has outlined, from the routine maintenance required in calm seas and normal weather to the heightened precautions necessary in rough seas, heavy weather, extreme temperatures, and icy conditions need vigilance and proactive measures. You can contact the professional marine equipment and offshore equipment supplier Boomarine for more comprehensive information or first-class products.